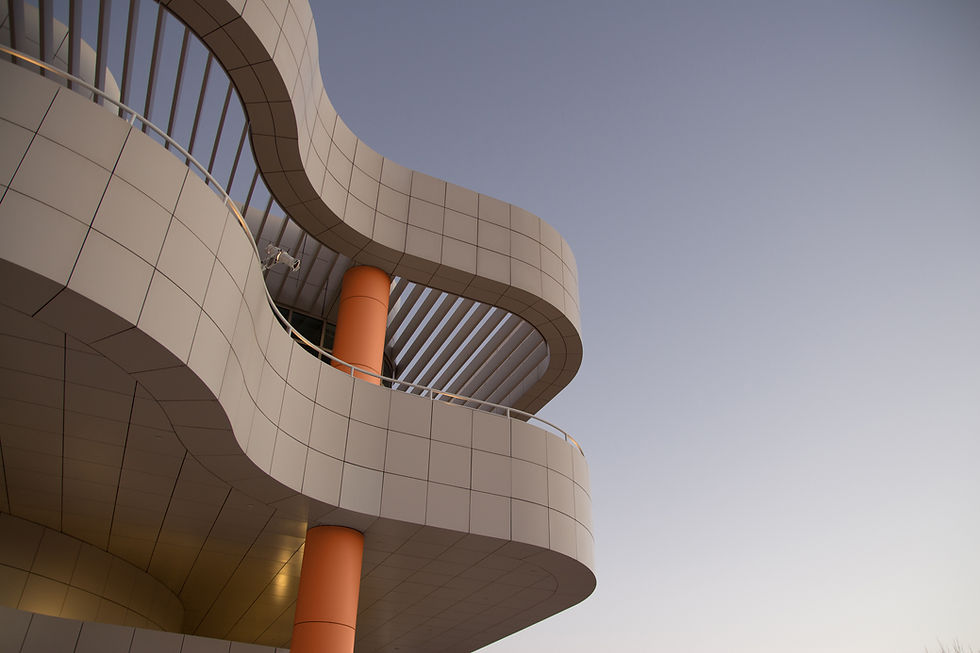
Control Strategies for Minerals Thickening (Part 1)
Jul 15, 2024
4 min read
We have discussed in early articles the strategies to optimize water consumption and learned the vital role that thickeners play in the optimisation of the water recovery process. Later, we also explored the most common problems that affect the operations and efficiency of thickeners. In this article, we will analyse the standard and advanced control strategies most commonly used in minerals thickening.
This post is divided into two parts. Part 1 will focus on standard control strategies while part 2 will discuss advanced control strategies.
Background
The thickening process is subjected to the feed flow and material quality perturbations, parameters that require to be controlled. The objective of control is to keep a stable % of solids in the thickener underflow discharge, while the internal layers of clear water, pulp interface and thickened mud bed (layer) (figure 1) are kept in defined ranges, and the mechanically operated torque is kept within safe operating parameters.
The variables used for control are defined below:
Input variables
The input variables are the main disturbances in the thickener and include:
Input volumetric flow variation (due to the change in the mill processing rate or variation in the metal grade),
Changes in particle size distribution, solids concentration and rheological conditions due to increased clay or mica minerals. Â
Output variables
The output variables are thickener parameters that must be kept constant or within a safe operating range. They are:
Concentration of solids in the thickener underflow discharge (density)
Suspended solids in recovered clear water (turbidity)
Clear water layer height
Mud layer height
Demanded rake torque
Process control variables
These are the variables that can be manipulated either manually or automatically to keep the output variables stable. They are:
Flocculant flow: allows to control the rate of sedimentation of particles by adding an agglomerating polymer.
Discharge flow: allows to control the height of the thickened mud layer/bed to modify the density in the discharge due to the variation of the compaction residence time. The way to control the mud/bed layer is by manipulating the speed of the pump or the discharge valve.Â
Standard Control Strategies
Currently in most medium-sized mineral thickening operations 10 to 50 ktpd, and even large operations greater than 100 ktpd, standard PID (Proportional, Integral, Derivative) control systems are used.
The basis of the PID controller is the processing of the error obtained by comparing the process variable with its respective target value or set point. The discrete PID controller calculates the output or effect action on the manipulated variable.Â
Control actions are governed by parameters known as proportional gain, integrative time, and derived time. It is necessary to properly adjust these parameters in order to control the output variables in the case of a step type change (abrupt change) of the reference as quickly as possible. In these standard control systems, output variables are prioritized, giving greater importance to the discharge density and turbidity of the recovered water.Â
Figures 2 and 3 show the control schematics of thickener underflow pumping and flocculant dosing control strategies. In figure 2, the thickener is operated automatically by a PI control of density or % solid discharge by manipulating the discharge pump. In figure 3, the clarity layer (clear water height) is used to maintain an acceptable turbidity in the overflow by manipulating the flocculant dosage.
Control strategies for minerals thickening- control underflow density using mud level.
Control strategies for minerals thickening - control of flocculant using clear water height
An example of the application of this control method is presented in figures 3, 4 and 5 in the operation of a 40m thickener processing 10,000 tpd tailings. The variation of the underflow and overflow output variables of the thickener are shown. Here the thickener is fed in average with an 8% solids slurry carrying 450 tph of tailings to achieve 67% solids in the discharge and less than 200 NTU turbidity in the clear water.
In a control period of 300 hours, the average values and standard deviation of the controlled variables are presented in Table 1.
The control system manages a variation of 7% in the tailings stream to maintain the % of underflow solids in the target with a 1% variation. However, in the overflow, there are periods in which turbidity values are above the target and there is also a risk period of high torque. The reason for this inefficiency is that there are other mineral and operational factors that do not respond to the flocculant as a control variable. For example, pulp yield stress, clear water level do not respond to increases in overflow water stream or rise rate (m3/h/m2).Â
Figure 5 and 7 show that hourly yield stress measurements (in the laboratory) correlate with the rake torque. However, this information is not used by the control system and the operator acts manually when a critical torque value is reached. To overcome these problems, advanced control strategies have been designed and are discussed in part 2 of this article.
Click here to read Part 2 of this article.
Explore solutions for common queries such as How do I control flocculant addition or How to optimise thickener control; by checking our SmartDiver® page.
For more information contact our technical team at sales@plapl.com.au or call us on +61 3 9786 1711