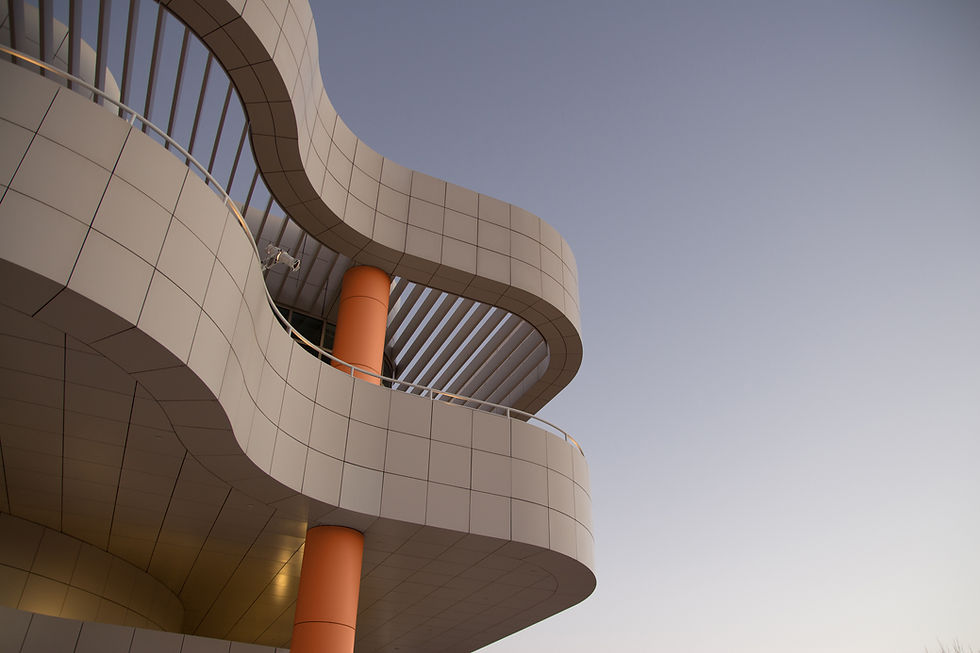
Case Study: Improved PAL Thickener control reduces Flocculant usage by $80,000 over six months with SmartDiver® System Integration
Jul 22, 2024
3 min read
Australia Nickel Refinery upgrades its PAL thickener by installing a new SmartDiver® system and integrating the output signals to its DCS to enhance its thickener control strategy.
CHALLENGE
Australian Nickel Refinery needed to improve thickener control to:
Increase underflow density
Decrease flocculant usage
Increase clarity
SOLUTION
Installed SmartDiver® system which provides measurements of clarity, hindered interface level and mud level as well as density trends of the compacting mud layer, allowing the thickener control strategy to be enhanced dramatically.
By monitoring the two independent layers of interface and mud, reliable process data was provided for:
1. Control of the underflow pump to optimize the underflow density, and
2. Control of the flocculant dosing system
The control strategy also implemented feed-forward control for the mud level and model predictive control for the flocculant addition.
RESULTS
Flocculant usage was dramatically decreased. Underflow density increased as it did clarity. Thickener operational down time was reduced.
Flocculant usage dropped from an average 121.78gt-1 to 69.94gt-1 resulting in a cost saving of $80,000 over six months, assuming a flocculant cost of $350 per kg. An added benefit of improved control was an increase in average flow rate, an increase in production due to less downtime and tighter operational parameters.
The first process that was automated on the thickener was the discharge rate of the underflow pump system to maintain the dense slurry compact bed at the optimum level in the thickener.
The PLA SmartDiver® mud level measurements were used in a basic slow acting PID feed-back control loop to manipulate the mud level. With this acting as a verification of mass balance control loop, feedback went directly to the VSD on the underflow pump.
There was a maximum mud level run in the tank, based on historical data of rake torque. This was set, and the SmartDiver® provided the process variable for the controller to control the underflow pump speed.
Maximum mud level, rake torque and underflow density were also used as inhibits.
The second process that was automated on the thickener was the control of the hindered layer settling zone or interface layer.
Interface changes can happen much faster, so a PID feed-back control was used, but on a faster acting loop. The feedback from the SmartDiver® interface reading trims this gram per tonne ratio. Here the flocculant flow was manipulated using differential interface control: the difference in mud and interface level (ie adjusting the flocculant addition to maintain a constant interface height above the mud).
The changes made to the control strategy reduced flocculant usage dramatically as shown in Table 1 and Graph 1.
|
Table 1: Decreased Flocculant Usage
Flocculant usage was reduced by around 40% over six months with underflow density being retained. Additional improvements to be looked at include reducing flocculant consumption even further, and controlling the PAL thickener with increased mud levels, with a view to increasing underflow densities.
Explore solutions for common queries such as How do I control flocculant addition or How to optimise thickener control; by checking our SmartDiver® page.
Reduce Flocculant usage with SmartDiver® - Email: sales@plapl.com.au or contact your local PLA Process Analysers representative to learn more.