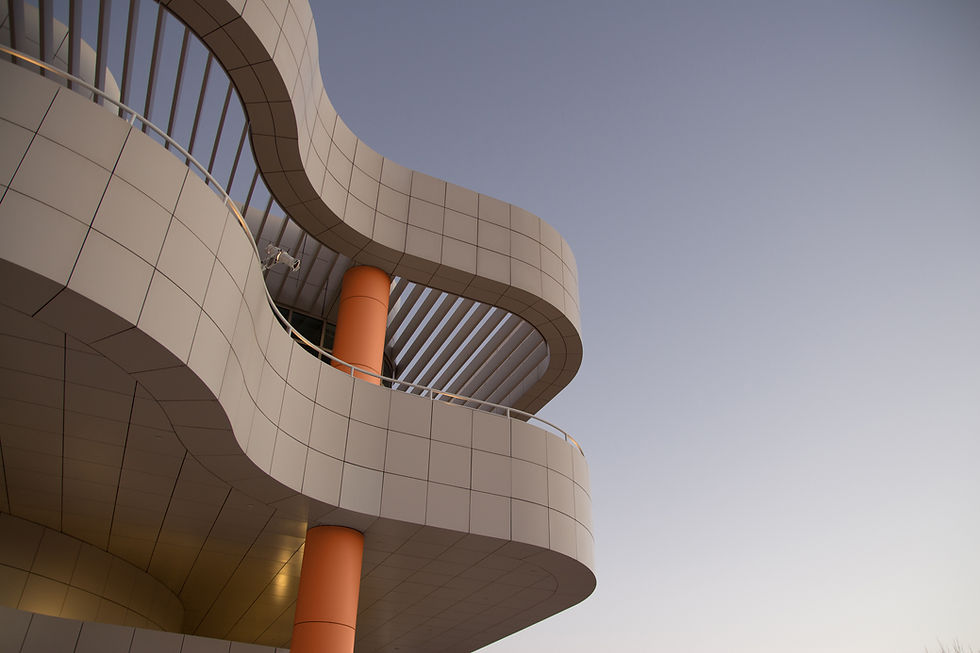
The Science of Bed Levels & Settling Zones: Decoding Thickener Performance
Mar 20
8 min read
In the world of Mineral Processing, Thickeners play a crucial role in dewatering suspensions — yet their performance remains one of the most misunderstood and under-optimised aspects of plant operations.
While most of the historical research has guided enhanced Thickener designs & Flocculant chemistry, recent research has revealed that one often-overlooked factor — understanding the Thickener’s settling zones.
In this article, we will be merging insights from key research papers to explain how understanding bed levels, Thickener zones and bed formations can lead to more efficient dewatering processes in Mineral Processing.
Overview – Settling Process
Thickeners operate on a fundamental principle: gravity-driven separation of solids from liquids based on density differences. As solid particles settle toward the bottom of a Thickener tank, clarified liquid rises to the top. This seemingly simple process becomes increasingly complex at higher solids concentrations.
When particles move closer together, their interactions intensify, causing settling rates to decline. At a critical concentration threshold—known as the gel point—the slurry transforms from individual settling particles into an interconnected structure. This network formation marks a crucial transition in the dewatering process, as particles begin supporting each other and forming a semi-solid bed. Beyond this gel point, further liquid removal occurs through compression rather than simple settling, requiring different approaches to achieve additional dewatering.
Understanding this process is key to optimising Thickener's performance. Early research by Coe and Clevenger, 1916 laid the foundation by identifying the four settling zones within a Thickener, while a century later, Crust’s quantitative studies and Vietti and Dunn’s work on mud bed interface control — has revealed how crucial it is to measure and manage these zones with precision.
These studies have significantly improved our understanding of Thickener variables, for instance, Crust in his thesis states:
Traditional models often underestimated solids flux — in some cases by as much as a factor of 100!
This wealth of knowledge now presents an opportunity for mineral processing operations to significantly enhance Thickener's performance.
Understanding Thickener Zones and Their Importance:
In 1916, Coe and Clevenger pioneered the understanding of thickening by describing a model with distinct zones within a Thickener, which is still referenced today. These zones provide insight into how particles settle and dewater in a Thickener:
Here’s a breakdown of the typical Thickener zones:
Zone A – Clarification Zone
The uppermost layer of the tank, where the liquid has largely clarified and is ready to be removed as overflow. The goal here is to maintain clarity and prevent suspended solids from escaping.
Zone B – Settling Zone
Beneath the clear liquid, solids begin to settle under gravity individually through the slurry. Solids concentration gradually increases with depth, causing settling rates to progressively slow. Flocculants can be added here to enhance aggregation and speed up settling.
Zone C – Hindered Settling Zone (Mud Level)
As the solids concentration continues to increase, particles begin interacting and interfering with each other’s movement. At the gel point — the slurry forms a loosely structured bed. From this point onward, the solids no longer settle freely and begin to compress under their own weight.
Zone D – Compression Zone (Heavy Mud)
At the bottom of the tank, the compacted solids form a dense, almost immobile bed. This zone represents the final stage of dewatering, where gravity alone is no longer sufficient, instead, compression forces drive out the remaining liquid as particles are squeezed closer together under the weight of the bed above. Additionally, mechanical pressure (Rakes) is often applied to achieve the desired underflow density.
These zones aren’t static — they shift continuously depending on feed conditions, flocculant performance, and operating parameters. That’s where bed level measurements become critical.
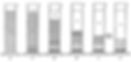
Understanding Bed Levels and Their Importance:
Now that we’ve explored the different zones within a Thickener, let’s delve into the importance of bed levels and how they influence these zones.
A bed level refers to the boundary between settling zones, particularly where the transition from free settling to hindered settling or compression begins. Monitoring these levels gives operators real-time insight into how the Thickener is performing internally — even though these zones are not visible from the outside.
Understanding the Thickener zones and bed levels is crucial because they directly influence key performance metrics, such as:
Solids Flux:Â The rate at which solids settle through the Thickener.
Underflow Concentration:Â The density of the solids discharged from the Thickener.
Residence Time:Â The time solids spend in the Thickener, which affects dewatering efficiency.
Steady-State Operation: When the feed rate, underflow concentration, and bed levels remain stable over time, ensuring consistent and predictable performance.
Â
Key bed level transitions include:
Interface Level:Â Moving downward from the Clear Liquor into the Settling Zone, there's a distinct boundary where solids concentration suddenly increases. This transition point marks where suspended particles first appear in meaningful quantities.
Mud Level: Where the flocculated particles begin compressing — the start of hindered settling. Operators use the mud level as a key control parameter, as it directly influences solid residence time, solids flux, and underflow concentration (Vietti & Dunn, 2014).
Heavy Mud Level: Also known as the Critical Compaction Point (CCP). This is where the pulp transitions from hindered settling to compression settling. Identifying this level helps operators to ensure that the underflow solids reach the desired density before being discharged.

Accurate Bed-Level Measurements will help operators to:
Maintain optimal settling zones for steady-state operation (Vietti & Dunn, 2014)Â
Adjust feed or flocculant rates based on actual zone behaviour
Prevent process upsets like overflow solids (Flaring), Rake Bogging or Donut-effects.
Control underflow density and maximise solids recovery

Importance of Networked Bed Formation
While understanding settling zones and bed levels is essential, the quality of the settled bed itself plays a pivotal role in determining Thickener efficiency. One key concept that often goes unnoticed — but has major operational implications — is the idea of a networked bed.
What is a Networked Bed?
A networked bed is a condition in which flocculated particles form a continuous, interconnected structure within the Thickener's mud zone. Instead of individual particles settling and compressing in isolation, they create a cohesive matrix that behaves more like a porous, semi-solid material. This structure can withstand internal stresses without collapsing, leading to a more stable and uniform compaction process.
By contrast, an un-networked bed consists of loosely arranged aggregates with weak inter-particle contact.
Negative outcomes from an un-networked bed:
o  The bed structure is weak and prone to collapse.
o  Poor rake-ability
o  Poorly defined zone boundaries
o  Uneven density distributions throughout the Thickener
Crust’s1 thesis notes that a networked suspension can densify about 5% more, compared to shearing un-networked aggregates.
How to ensure a Networked Bed is formed?
Forming a networked bed requires careful control of several key factors:
Maintain Adequate Bed Height: The height of the settled solids bed (mud level) is an important benchmark. Research1Â suggests that a bed height of at least 2-3 meters (of a 5m Thickener) is often necessary to achieve a networked state. At these depths, the pressure at the base of the Thickener is high enough to compact the flocs into a stable, interconnected structure. If the bed is too shallow, particles may never reach the gel point, and the resulting bed will remain un-networked and inefficient.
Monitor Bed Levels: Regularly measuring bed levels, ensures that the Thickener is operating within the optimal range for networked bed formation.
Monitoring the 3 key variables of a Thickener: Optimising Flocculant Dosage and balancing between feed rates and underflow discharge rates are equally important to ensure a networked bed is formed.
Â
Visualising the Impact of Networked vs. Unnetworked Beds
To better understand the significant operational differences between networked and unnetworked beds, Figure 4 presents a comparative model showing how solids concentration changes with depth inside a Thickener for two different operating conditions.

Source: Optimisation of Thickener Performance: Incorporation of Shear Effects by Adam Anthony Holden Crust
Interpretation of Figure 4:
Y-Axis (Height of the Bed): This represents the depth within the Thickener, from the top (clarified liquid) to the bottom (compressed underflow).
X-Axis (Solids Concentration): This shows the concentration of solids (φ), which increases with depth.
The horizontal dashed lines represent key bed heights — the total bed depth (hb) and the point where the networked structure is achieved (hn).
Left graph (Unnetworked):
Solids concentration increases with depth but doesn't reach the gel point.
Underflow solids concentration is lower (φu = 0.18 v/v).
No networked height is observed (hn = 0).
Right graph (Networked):
Solids concentration increases with depth and exceeds the gel point.
Higher underflow solids concentration (φu = 0.30 v/v).
A networked height is achieved (hn = 0.89 m).
Â
These profiles show that the presence and height of a networked structure can significantly impact Thickener's performance. The gel point is a critical threshold for efficient dewatering, and it is only reached in a networked bed.
This reinforces the idea that there is a direct relationship between bed height and a networked system.
Importance of the Mud Level
With a clear understanding of networked bed formation, we can now examine how the mud level impacts Thickener's performance.
The mud level — the height of the settled solids or suspension bed — serves as one of the most critical control parameters. It represents the point where hindered settling dominates, and where the foundation for networked bed formation is established.
Figure 5: A model simulation comparing three mud level heights (1m - blue line, 2m – purple line, and 4m - green line) shows that:
As the mud level height increases from 1 meter to 4 meters, both the underflow solids concentration and solids flux increase.
Under-optimised beds (e.g., 1m) fall short of reaching the gel point, resulting in less efficient dewatering.
This demonstrates an important operational principle: higher mud beds generally enable better densification and higher throughput capacities.
The model predictions align with Crust's research showing that increased bed heights provide greater compression forces, extended residence times, and improved particle networking—all contributing to enhanced dewatering efficiency.

Source: Optimisation of Thickener Performance: Incorporation of Shear Effects by Adam Anthony Holden Crust
Conclusion: Accurate Bed Level Measurements - Turning Insight into Optimisation
Mineral processing operations are facing growing pressure to — improve water recovery to increase throughput and reduce flocculant costs. But as this article has shown, backed by Research from Coe, Clevenger, Vietti, Dunn, and Crust – true optimisation doesn’t come from guesswork or outdated assumptions. It comes from understanding the internal dynamics of the Thickener: the settling zones, the transitions between them, the formation of a networked bed, and, most critically, the accurate measurement of bed levels.
These insights confirm that bed levels are not just a passive result of operations, it’s an active control parameter. By accurately measuring and managing it, operators can shift from reactive adjustments to proactive optimisation, driving better performance.
To implement these valuable insights into real-world applications, the SmartDiver® addresses this necessity by providing continuous real-time measurements of various Bed Levels within a Thickener. The SmartDiver’s® Sensor takes readings of changes in Solids Density as it descends into the Thickener and charts the Interface, Mud Levels & Heavy Mud Levels.
SmartDiver® transforms complex Thickener behaviour into actionable insights.

For a real-world example of how bed level measurements can optimise Thickener operations, check out this case study: Improved PAL Thickener control reduces Flocculant usage by $80,000 over six months with SmartDiver® System Integration
In short, investing in reliable measurement technology and integrating it into operational strategies can significantly improve yield, reduce costs, and enhance process stability. Especially when technologies like SmartDiver® make this data accessible, the opportunity to improve is firmly within reach.
Â
Contact the PLA Team to discuss the integration of the SmartDiver® in your Site or arrange for a Free Site Trial at sales@plapl.com.au.
Glossary:
φ (solids concentration) Â
φg (gel point) Â
φu (underflow concentration) Â
A(z) (parameters related to height)Â Â
Dagg,∞ (aggregate densification parameter)
Citations:
Adam Anthony Holden Crust (2017): Optimisation of Thickener Performance: Incorporation of Shear Effects. Particulate Fluids Processing Centre - Department of Chemical Engineering - The University of Melbourne, Australia.
Coe, H. S. and G. H. Clevenger (1916): Methods for determining the capacity of slime settling tanks. Transactions of the American Institute of Mining Engineers.
A.J. Vietti and F. Dunn (2014): A description of the sedimentation process during dynamic Thickener operation. Australian Centre for Geomechanics, Perth.
Prof. Dr. Jabbar H. Al-Baidhani (2018): Hindered (Zone) Settling Type (3) Settling. University of Babylon.
Keywords: Science of Bed Level Measurement, Settling Zones, Mining, Australia, How to reduce Flocculants, How to optimise Thickeners Clarifiers, Save Water in Solid Liquid Separation Process, Mineral Processing, Metallurgy, Energy, Material Science