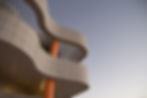
Most common problems in Thickener operations (Part 1)
Jul 11, 2024
4 min read
We have discussed in early articles the strategies to optimize water consumption (part 1 and part 2) and learned the vital role that thickeners play in the optimization of the water recovery process.
In this blog, we will explore the most common problems that affect the operations and efficiency of thickeners. The blog will be divided in two parts. Part 1 will cover problems in thickener operations caused by thickener design errors and changes in ore properties.
Part 2 will discuss in detail the problems caused by mechanical and maintenance issues (including issues with thickener instrumentation and control) and what can be done to solve them.
Thickeners are continuous sedimentation equipment used to perform solid-liquid separation in finely ground slurry ore as mineral concentrates or tailings (figure 1).
Depending on the configuration of the plant, the type of mineral and the thickener technology, the recovery of water can vary between 65% to 95% of the process water, as shown in figure 2.
The main problems that operators face include the presence of suspended solids in the recovered water and the density or percentage of solids of the thickener discharge outside the set targets. These problems are classified according to whether they are caused by thickener design errors, changes in ore properties, or mechanical and maintenance issues.
1.    Thickener design errors
In thickener design, there are two specifications that will define the tank efficiency to process minerals: thickener area and drive torque. These specifications commonly have high variability and are required to adjust to the programmed processing tonnages during the life of the mining project.Â
Â
Thickener area
The thickener area depends on the mineral sedimentation rate (m2/t/d) or the specific feed rate (t/h/m2) which are determined by laboratory or pilot testing. These tests are carried out with representative samples of mineral and different granulometry. The tests also evaluate different dosages of flocculant.Â
Additionally, the selection of an adequate safety factor that represents the variability of the mineral to be processed must be considered. The safety factor can vary between 1.15 and 1.30.
Drive torque
The rakes drive mechanism has to apply a sufficient force for the rakes to move the slurry in the thickener. The torque of the mechanism is proportional to the degree of viscosity of the thickened pulp measured as yield stress. The relationship between %solids and shear stress is exponential so that small changes in %solids generate a progressive increase in shear stress, and consequently the required torque. Figure 3 shows a rheology curve for copper ore tailings.
Based on this data, thickener suppliers apply safety factors that define the torque factor (K) as per below:
In the event that mistakes of under sizing the area or torque have been made, the thickener operation will have capacity problems and will not meet the thickening target.
Â
Common design errors
Design errors appear after start-up when flow throughput or rheology variations exceed applied factors. The main design errors include:
Lack of capacity of the feeding launder
Less thickener area
Lower drive torque
Smaller feed-well diameter
Lower capacity pump discharge
Larger diameter of the discharge pipe (underflow). This produces mineral settling
2.   Changes in ore properties
The ore fed to the thickener is essentially variable due to changes in upstream operations (mined sector, milling and concentration). The main changes that affect the thickener are: throughput variations, particle size variation, increase in coarse mineral and clay and ultrafine content variation.
Â
Throughput variations
Due to changes in hardness and ore grade, the tailings and concentrate treatment rate change hourly. An automatic control system is necessary to keep the operation of the thickener stable, along with the use of online monitoring of the clear water and pulp phases inside the thickener. These layers can be monitored with systems such as SmartDiver and can be used to automatically control throughput variability. Â
Particle size variations (settling rate variation)
The sedimentation rate is strongly influenced by the particle size, so that the variations in the grinding stage are transferred to the thickening stage. When very fine ore is fed, the settling rate decreases which in turn can create issues such as increase in torque, clear water contamination and decrease of the % solids in the discharge.
 Â
Coarse mineral
Increase in coarse mineral (particles greater than 0.5 mm), as a result of plugging of the hydro cyclones, can create problems at the bottom of the thickener, increasing the torque required sometimes damaging the rake drive mechanism.
Clay and ultrafine content variation (rheology change)
When the content of fine particles (clays or micas) increases more than 20% above their normal value, due to their high specific surface, problems of excessive increase in rheology are generated e.g. viscosity and shear stress increase making thickening difficult. Mine planning is necessary to control the fines content under the specified values in the design.
Our next blog, most common problems in thickener operations (Part 2), will discuss in detail the operation problems that originate in mechanical, and maintenance issues (including issues related to instrumentation and control).
For more information contact our technical team at sales@plapl.com.au or call us on +61 3 9786 1711.